Optimizing Coating Excellence: Surface Preparation Blasting Techniques for High-Quality Finishes
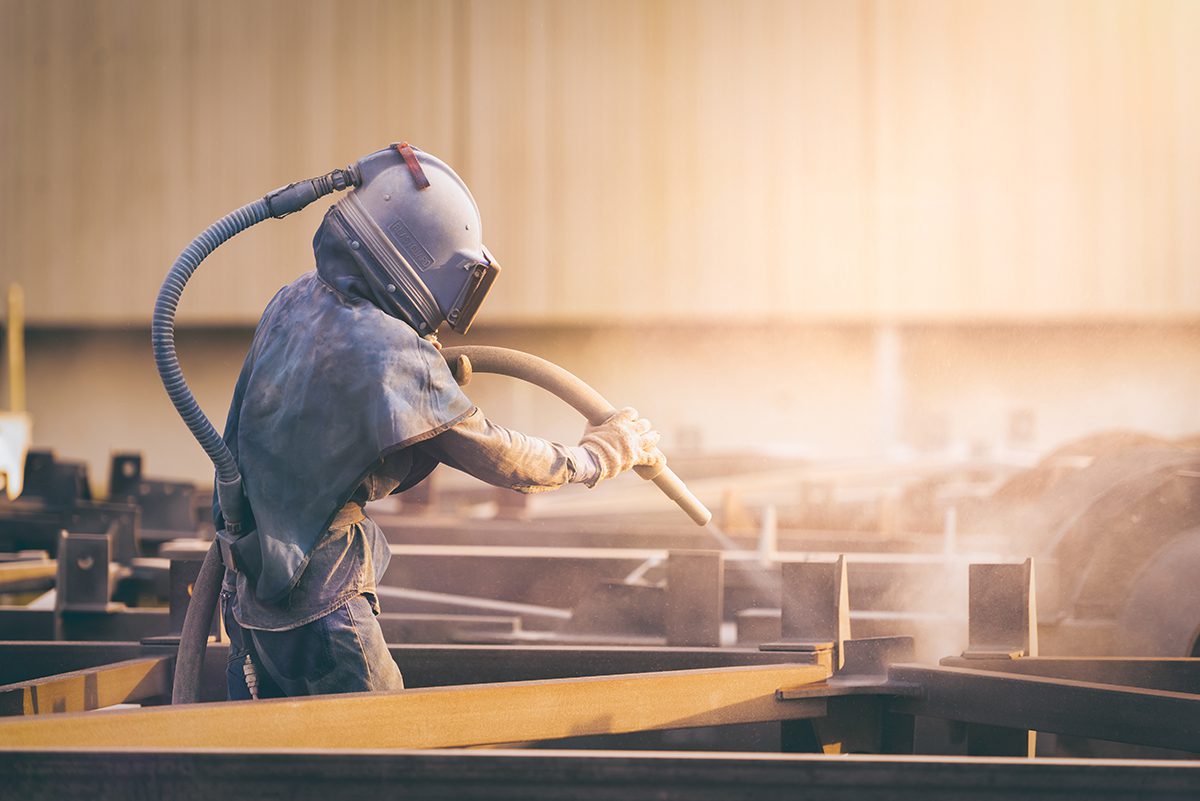
When you reach for your favorite tool, you want to know that the grip will be secure. Loose and insecure coating adhesion could cause work errors or even physical harm. It isn’t enough that an unstable coating system can be unattractive or lead to rusting. Poorly performed coatings can be dangerous as well.
Surface preparation blasting is one of the primary methods that will provide your goods and tools with more secure and effective coatings of all kinds. Proper surface preparation methods are essential to the process of bringing out the best in the metal parts and pieces you bring us.
What Is Surface Preparation?
Surface preparation is a manufacturing process that ensures maximum adhesion and even layering of coatings. If you’ve ever gripped a hammer or screwdriver and noticed an uneven surface on the grip, this is likely due to poor surface preparation.
There are multiple surface preparation methods, but one of the most common is abrasive blast cleaning. This method essentially sand-blasts the material surface to smooth out the surface and clean it. Many different abrasives are used for blast cleaning, with unique grits and specifications for how the surface should look after blasting.
What Are the Benefits of Surface Preparation Blasting?
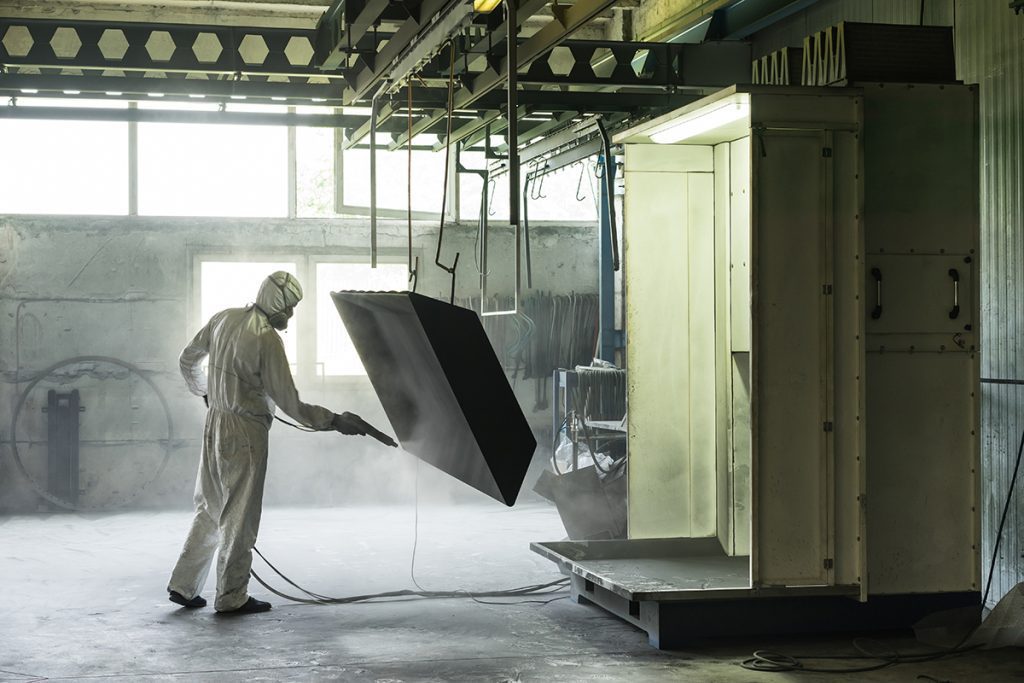
Surface preparation methods ensure that coatings of all kinds will be successful. For aesthetics, you want a smooth finish, but even more importantly, an effective coating is needed for safety, protection, and durability. Chemical tanks must hold potentially dangerous materials without failure, and medical instruments must stay sanitized.
Without prep, a coating could quickly wrinkle or loosen or even begin falling off immediately. Coatings often cure for added bondage, but surface preparation is needed for maximum adherence. Surface preparation cleans away contaminants but also provides a surface that has a rougher surface profile.
How Is Surface Preparation Done?
Surface preparation in a coating shop will generally follow these steps:
Surface Assessment
Before any blast or chemical cleaning is done, the surface is inspected to determine if cleaning is even viable. When rust or surface contaminants are too deep, cleaning may cause more harm than good.
Thorough Cleaning
When preparing a surface, the material’s surface needs to be as clean as possible. Oils, dirt, and other surface contaminants can interfere with the preparation or even react with the coating itself. Proper surface preparation will ensure no chlorides, acids, or prior coating are present.
Remove Loose Material
Even if the piece is no longer rusting, damaged or loose pieces may be removed. The blasting process can effectively remove loose rust and weak material.
Re-Profile the Surface.
The piece should be re-examined to affirm that it will still take to the coating. Over the course of blasting and cleaning, the part’s geometry could have changed. Profiling the surface ensures that the coating will be optimally chosen.
Dry the Surface
The coating adheres best to a dry surface. Moisture, even when minor enough to be invisible to the naked eye, can expand when heated during the curing process, causing bubbles, holes, or other errors. Trapped moisture beneath a coating can also hasten rust and corrosion, negating most powder coating benefits.
Surface preparation will make sure that your coatings are well applied. This ensures a coating that has a long lifetime and maximally applies its benefits, whether they are medical, industrial, or other protective coatings.
What Types of Surface Preparation Blasting Are Done?
As stated before, abrasive blast cleaning and surface preparation utilize a jet of compressed air impregnated with abrasive particles. This jet effectively removes surface materials such as old paint or coatings, rust, and impurities at the surface. Abrasive blasting is common in many industries, which has resulted in a wide range of abrasives being used for unique effects.
Light Blasting, Light Sweeping, or Brush Off Cleaning
The lowest intensity form of abrasive blasting usually removes looser and larger surface materials. This level also has the added benefit of creating a rough surface that will provide more for the coating to adhere to. This type is sometimes referred to as SP 7 surface preparation because of the standards applied to it. This is common for re-applicating old liquid or powder coatings.
Industrial Blast Cleaning
Industrial blast cleaning is higher-intensity and intended to remove more tightly adhering matter but leave behind existing coatings that need to be updated. This tier of blasting will not remove material-level shadows, streaks, or stains that will usually form after a piece is forged or molded. This is a very common method due to the cost-to-benefit ratio.
Commercial Blast Cleaning
Commercial abrasive blasting is intended to remove 100% of surface material and some of the shadows and stains from the surface. This is often referred to as SP 6 surface preparation or NACE 3 commercial blast cleaning because of the standards of quality that should be reached. This is very common in industrial coating applications.
Near-White Metal Blast Cleaning
Near white blast cleaning is 100% effective at removing adhering material such as preexisting coatings. This also effectively removes nearly all stains and shadows from steel surfaces. This is commonly used to prepare high-performance coatings that need to resist corrosion. SP 10 Surface preparation is another name for this process.
White Metal Blast Cleaning
This is the highest-intensity abrasive blasting, with the goal being a complete removal of all surface material, mill scale, shadows, and stains. This ensures a surface preparation that is as clean as possible for high-performance coatings that pose danger if they fail, such as chemical tanks, turbines, and nuclear reactors. This is known as SP 5 surface preparation.
Dry blasting is very common, but for technician safety, these blasting methods can also be wet. Wet abrasive blasting introduces moisture into the jet stream to reduce dust and fine particles in the air.
What Are the Standards for Surface Preparation?
The major organization that issues standards for coatings and surfaces is the Association for Materials Protection and Performance (AMPP). This organization is a merger between two organizations whose names are still used in standards: The National Association of Corrosion Engineers (NACE) and the Society for Protective Coatings (SSPC). The following is an at-a-glance view of what the four most common standards demand:
Removes Dirt, Oil, etc. | Removes Old Coating | % of Stains Removed | |
NACE 1/SSPC-SP5 | 99% | ||
NACE 2/SSPC-SP10 | 95% | ||
NACE 3/SSPC-SP6 | 33% | ||
NACE 4/SSPC-SP7 | X | X |
These standards for surface preparation blasting have provided manufacturers, coating companies, and consumers with better safety and quality control expectations across all industries. Following these standards is a basic expectation of any coating business.
Call Today for Coating Excellence
Metal and steel surfaces of all kinds require preparation before any coating can be applied. With this kind of protective coating, you can avoid corroded and rusted containers, damaged goods, and broken equipment. Surface preparation techniques can ensure this coat lasts longer and will adhere properly.
Abrasive blast cleaning and the surface preparation blasting process can ensure that your products are ready and optimal for the protective coating that we can apply. These processes and standards can be difficult to navigate, so trust a leader in the field to apply the best method, achieve the best standards, and give you the best results.