What Coating Offers the Best Marine Corrosion Protection for New Steel?
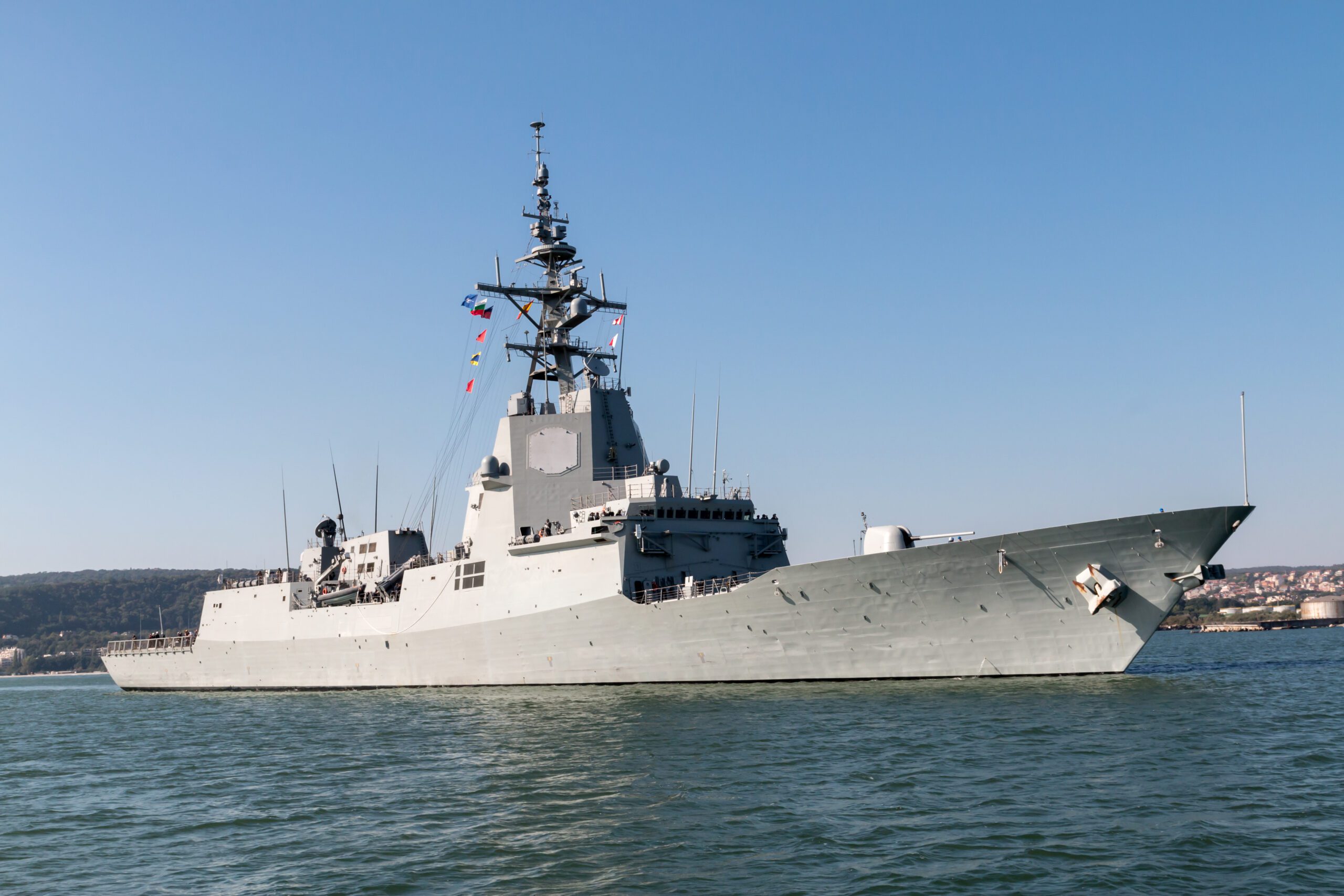
There is no doubt that steel is a superior product for marine applications. It’s relatively low cost, extremely strong, and an easy substrate to fabricate into specific designs. Yet, its drawback is that when exposed to the harsh conditions of saltwater, the material begins to rust, jeopardizing the integrity of the ship or other marine apparatus.
That’s why manufacturers who make steel products for the water need appropriate marine corrosion protection to keep the inherent durability properties of the substrate intact. Four popular anti-corrosion options include cathodic protection, painting the surface, galvanizing the steel, and powder coating the product. Each comes with advantages, but there is one clear winner: fluid bed powder coating.
Here at Precision Coating Technology & Manufacturing, we have been helping product designers and manufacturers for over 30 years get the powder coating protection they need to create long-lasting, durable products that are resistant to corrosion, abrasion, and wear. Learn more about why powder coating is the best option and how we can help protect your ships, boats, brigades, pontoons, and other water apparatuses from marine corrosion.
The Unique Challenges Faced by Marine Products
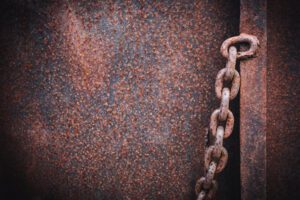
Many industries, like aerospace, agricultural, hydraulics, and defense, require sophisticated coatings on their tools, machines, wiring, and more to protect them from compromising assailants. From wear and abrasion to corrosion and outdoor weather, these trouble-makers weaken the strength of the products, making safety a top concern. But marine products face another set of challenging conditions—saltwater.
Since these products spend most of their lives bobbing on the surface of saltwater, protecting steel against the corrosive power of saltwater is a top priority. Corrosion is an electrochemical reaction that leads to rust. Rust degrades the metal, thus leaving it vulnerable to failure.
These products can also face extreme temperatures, strong winds, chemicals, and other conditions that can cause corrosion to happen quicker. And when lives are on board those ships, if the steel fails due to corrosion and isn’t caught in time, those lives are at risk.
Types of Marine Corrosion Protection
As a result of this problem, many marine manufacturers look for anti-corrosion sprays or coatings for navigational apparatus. But which one will provide the best performance? Let’s look at four primary types of marine corrosion protection coatings, each with advantages and disadvantages.
1. Cathodic Protection
Cathodic protection suppresses the electrochemical reaction taking place when a steel product is exposed to corrosive conditions, like saltwater. A negatively charged electrode, called an anode, releases electrons, and oxidizes during the electrochemical reaction, thus drawing it away from the positively charged electrode, called the cathode. This process makes the structure cathodic and lessens the corrosion on the steel product.
One way to use this marine corrosion protection is by using a sacrificial anode. The slower-corroding metal becomes the sacrificial anode by pairing the steel with a metal that will corrode slower, like zinc, nickel, cadmium, or aluminum. For example, pairing steel (the cathode) with zinc (the anode) causes the zinc to oxidize when exposed to water, and draws the reaction away from the steel, thus protecting it.
The problem with sacrificial anodes is that when the zinc is wholly eroded from rust, the steel is exposed and susceptible to corrosion.
2. Paint
Paint, especially ones that contain high levels of active zinc, is another way to provide marine corrosion protection. Marine corrosion spray coats the steel water apparatus to protect it from oxidation. However, like with a sacrificial anode, the paint will eventually chip, wear, or scratch from the harsh saltwater. In the end, your steel is still exposed unless you remove it from the water and repaint it routinely.
This process is costly, time-consuming, and wasteful of resources. Your steel boats, oil platforms, ships, and other water-based machines are still going to face corrosion even if you coat them with anti-corrosion spray paint for marine apparatus. Additionally, the water, sunlight, and heat will break down the paint quicker, thus exposing the steel much faster than using another method to prevent corrosion.
3. Galvanizing
Galvanizing is the process of applying layers of zinc onto a surface for protection from corrosion. This method of preventing corrosion requires the product to go through several chemical baths to remove scale, grease, grime, and rust. It is then dipped into a tube of molten zinc and hung to dry.
The problem with galvanizing your steel is that the chemical baths don’t remove all the contaminants. And if all the impurities aren’t removed, then the zinc coating can’t adhere as well to the substrate. Without that proper adhesion, you risk stripping away the galvanized layer in the harsh conditions of saltwater, and, like with the other methods for marine corrosion protection, the steel gets exposed.
4. Powder Coating
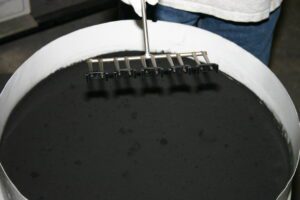
Powder coating, particularly fluid bed powder coating, provides a thick, substantial layer of marine corrosion protection to your steel ships. Using finely ground powder particles in a bed with a porous plate at the bottom, air passes through the plate and suspends the particles in a fluid-like state. The heated steel product is then dipped into the powder bath, allowing the melted particles to form a fused film onto the part.
Fluidized bed dipping provides excellent, full coverage for even large, complex pieces. The thick layer provides the protection your steel marine apparatus needs to resist corrosion and maintain its structural integrity. Before dipping, the part is prepped by removing scale, grime, grease, and existing rust through a specific surface treatment that ensures a durable, bonded finish on your powder-coated product.
Which Anti-Corrosion Coating is Best for Marine Applications?
There is no other choice than powder coating when you’re looking for the best marine corrosion protection method. With powder coating from PCTM, the thick layer of protection is adequately adhered to the steel substrate, slowing the corrosion rate better than any other method. With cathodic protection, painting, and galvanizing, the protective layers are all subject to degradation over time, requiring frequent re-applications of the protective coating.
In addition, powder coating can come in multiple colors, so it is both eye-pleasing and functional. And since powder coating is environmentally friendly with no waste or emissions, you can feel good about this marine corrosion protection.
Who Can Powder Coat My Marine Product?
Precision Coating Technology and Manufacturing, of course! Located in the heart of Pennsylvania, our team is well versed in solving everyday challenges various sectors face, including the marine industry. With our powder coating process, you can rest assured that you will have the marine corrosion protection your items need for long-lasting and durable coverage that withstands even the harshest water conditions.
Get in touch with our experienced team today to see how we can help solve your corrosion problems and protect your metal surfaces with a high-quality finish!